For business class seats, an airy, spacious future is being designed
CNN/Stylemagazine.com Newswire | 10/8/2020, 10:01 a.m.
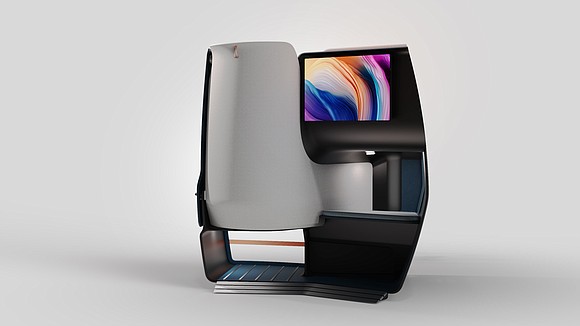
By John Walton, CNN
(CNN) -- There's an airy, spacious, futuristic seat coming to business class, with all-new scientifically engineered structures and materials borrowed from Formula 1 cars.
It's a completely new high-tech monocoque called Airtek from JPA Design, the people who redefined business class for the modern age a decade ago, and it's going to change the way business class cabins look and feel.
What this new monocoque revolution means when you travel is more space, lighter seats leading to a smaller carbon footprint and more reliable seats with fewer moving parts to break.
"A monocoque is a term and approach inspired by the automotive racing industry. It's really a unification of structure and other components that are around it -- rather than having an independent metal structure, independent composite furniture, independent seat, independent frame, all these all these different parts -- by unifying them into a single highly efficient composite body with no wasted space," says JPA's Creative Director Elliott Koehler.
To get there, the plan is to have the seat structure entirely made of composites, which will make it incredibly strong for its weight. That also crucially removes a lot of structure from the place where your feet, knees and even your pieces of hand luggage go.
"The benefit to the passenger would be enormous in terms of leg room, and the ability to store a full sized cabin bag in the seat right in front of them," Koehler says. "That would mean the reduction or removal of overhead bins, further reducing the weight of this airplane. And of course, less bins means a much more open cabin."
Shedding the weight of present-day business class seats
Today's business class seats are made up of a lot of individual parts, metals and thermoplastics and a few small bits of composite material, all fixed together with bolts, screws, glue and rivets. That's an involved process that requires a lot of engineering management to ensure it goes well.
If it goes wrong, and the seat is produced late or it doesn't work properly, you end up with an airline's latest, greatest airplanes with their latest, greatest business class cabins parked on the tarmac because the business class seats either aren't ready to install or are out of service and need to be fixed.
These seats are also very heavy: a multipart business class seat can be north of a hundred kilos (220 pounds) and first class seats even more. It's not just the size and materials, it's also how they're fixed together.
JPA is working with Williams Advanced Engineering and SWS to create Airtek, and the companies are targeting a minimum of 10% and as much as 20% weight reduction through using the monocoque composite structure.
Williams, a name which Formula 1 fans will recognize, is a technology and engineering offshoot of the racing team, while SWS is a certification outfit specializing in airworthiness of cabin products.
A seating solution in line with Covid-19 sensibilities
In recent years, many airlines have been providing more storage for bags and even jackets around business class seats, in small storage lockers, under ottoman footrests and even in individual mini-closets.
In the age of Covid-19 and with passengers unlikely to suddenly stop caring about cleanliness and hygiene, travelers may come to appreciate a lack of shared facilities such as overhead bins, and indeed during the pandemic some countries have even discouraged or banned their use by passengers.
"We're keeping things really open" in the Airtek seat, Koehler explains.
"There's a little storage for a laptop that's remarkably open, so you can see it's a clean and a safe place to put your electronics. The coat hook is just this very minimal strap, almost like a piece of footwear fashion. So that keeps it super clean, and super open and super lightweight. So everything a passenger sees as they're looking around this seat will communicate this new vision -- a lightweight, but also a comfortable and new open experience."
While color and some finish selections are usually made by airlines, the team is also leaning into light-and-dark contrasts for styling the seat, which both makes for a bold design language for sighted users and a seat that is responsive to the needs of blind and partially sighted people.
Design innovations that work in the real world
A raft of new technologies will help the team to make the seat lighter, sturdier and more spacious, from resins to thermoset and thermoplastics.
The secret sauce, Koehler says as we dive into the technical details, is "the way we are intending to combine them with the manufacturing processes being selected. This enables a more flexible structure to be produced, allowing for the management of the critical mechanical pitch and roll pre-loads, whilst allowing for quick cycle times and the use of recycled materials. This is where [Williams'] experience within composite design and use for the automotive and motorsport sectors has played a crucial role."
But it's also about making sure that this high-tech wizardry works in the real world.
Aviation has its own version of Prussian Field Marshal Helmuth von Moltke's epigram "no plan survives contact with the enemy" -- "no product survives contact with the passenger". That can also be expanded to "or the cleaners" in the time of coronavirus, as increased cleaning and even UV light sterilization can pose long-term structural durability issues to certain composites.
As ever with completely new seats, part of the challenge will be ensuring that it can be certified as safe, given that they must be able to withstand 16g impacts -- that's 16 times the force of gravity -- while protecting their occupants.
That's where SWS' certification expertise and JPA's decades of seat work on previous generation products such as 2010's game-changing Cathay Pacific "herringbone" pod seat or Singapore Airlines' latest business class come into play.
The JPA team hopes to have a fully resolved model in place for April 2021 -- either in person at the annual Aircraft Interiors Expo or virtually, depending on the epidemiological situation -- to show their design off to airline customers considering their next generation of business class seats.